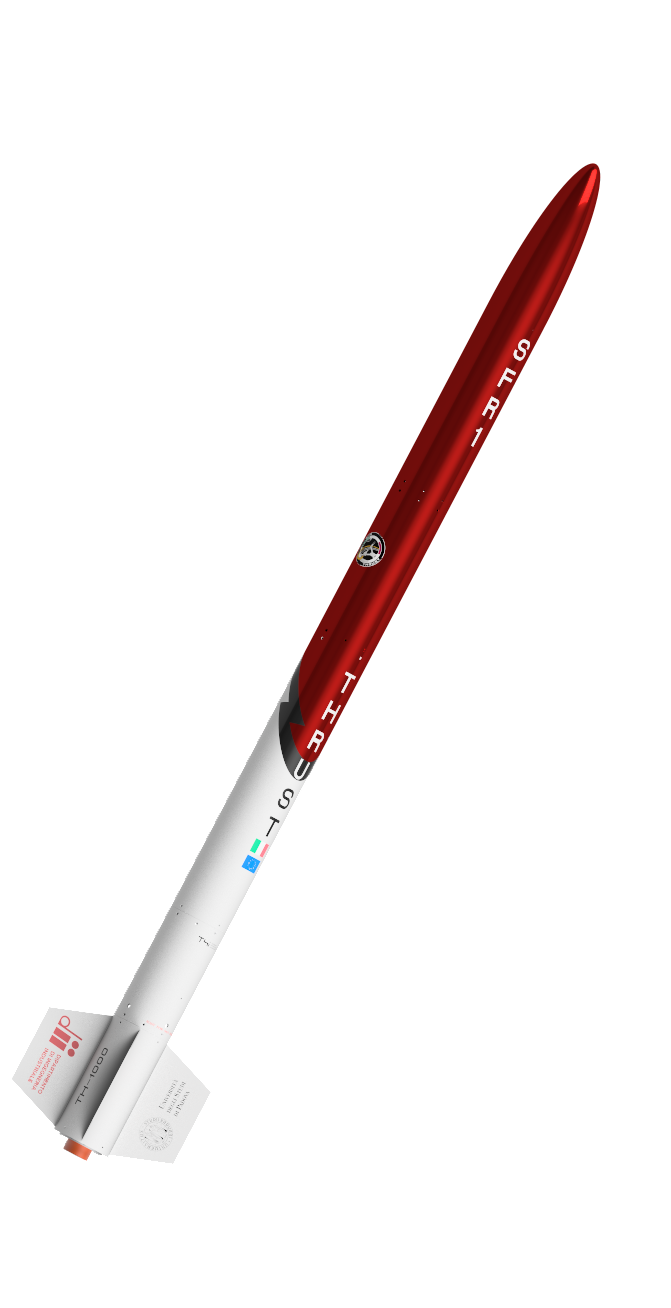
SFR 1
Hybrid Propulsion
SFR1 represents our first step into the world of aerospace technology. Designed and built entirely by our team, this rocket features a hybrid engine powered by paraffin and N₂O, combining safety, efficiency and performance. SFR1 is the result of months of engineering, testing, and innovation. Every component plays a crucial role in ensuring the rocket’s functionality, stability and safety. The avionics & payload section, often referred to as the “brain” of the rocket, is essential for remote ignition, telemetry and system control and can also accommodate an additional payload if needed. The nose cone is the first part to face the airflow during flight, making its aerodynamic design a critical factor in minimizing drag and optimizing performance. A dual-parachute recovery system, featuring an ejection mechanism entirely designed and developed by our team, ensures a safe return after launch. The welded aluminum propellant tank, operating at approximately 60 bar, houses the oxidizer and includes multiple safety mechanisms to prevent failures. The interstage section contains our team-developed main flight valve, which regulates propellant flow and enables precise control over the launch sequence. The combustion chamber, the “heart” of propulsion, is where high-temperature gases accelerate through the nozzle to supersonic speeds, generating the necessary thrust for SFR1 to take off. For a stable and controlled flight, SFR1 relies on its aerodynamically designed fins, preventing erratic motion and maintaining the rocket’s intended trajectory. In addition to building the rocket, we also developed the launch pad and ground segment for telemetry and mission control, ensuring complete oversight of every phase of the launch, from ignition to recovery.
SFR0
Technological Demonstrator
SFR0 was developed as a technological demonstrator, designed to test all subsystems except for the engine. This allows the team to verify and refine critical components in advance, ensuring a smooth launch as soon as the engine is ready. The rocket serves as a testbed for structural, recovery, and electronic systems. The structural elements being tested include the launch pad and the rocket’s outer skin. The recovery system features both a black powder and a CO₂-based mechanism to ensure a safe descent. The onboard electronics manage the activation of the recovery system and collect crucial flight data. In addition to testing these subsystems, SFR0 provides valuable data for the Mission Analysis Team. The team conducts Monte Carlo simulations to predict the rocket’s landing area and the actual launch of SFR0 helps assess the accuracy of these simulations, improving the overall reliability of the predictive models. By testing these key elements, SFR0 plays a fundamental role in preparing for future rocket launches, reducing risks and enhancing reliability.